Whitepaper
Lorem Ipsum is simply dummy text of the printing and type
Newsroom
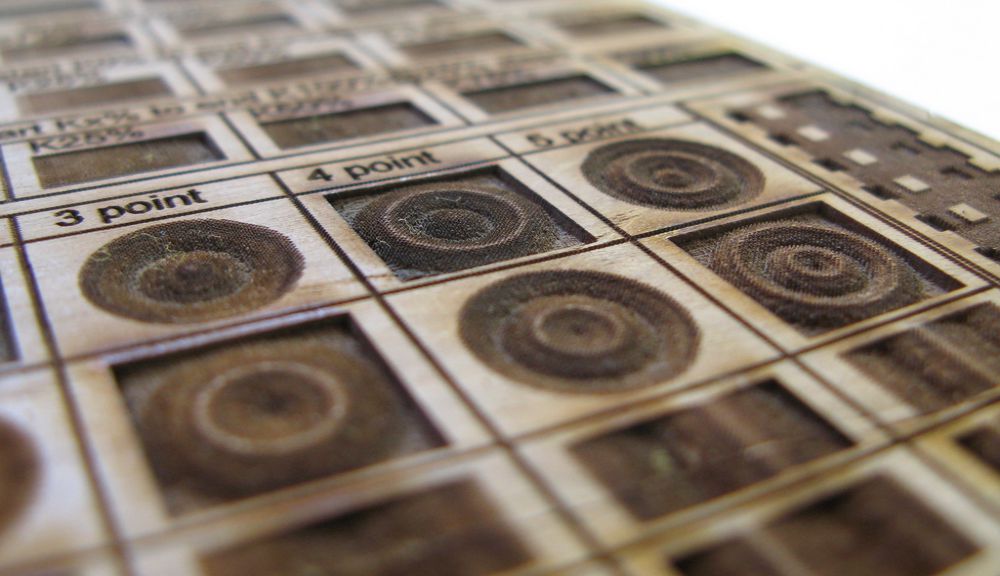
8 reasons why you should adopt a CO2 laser cutting system
In the last few years, laser-based processes have found application in nearly every sector. Practically every machining operation, that has
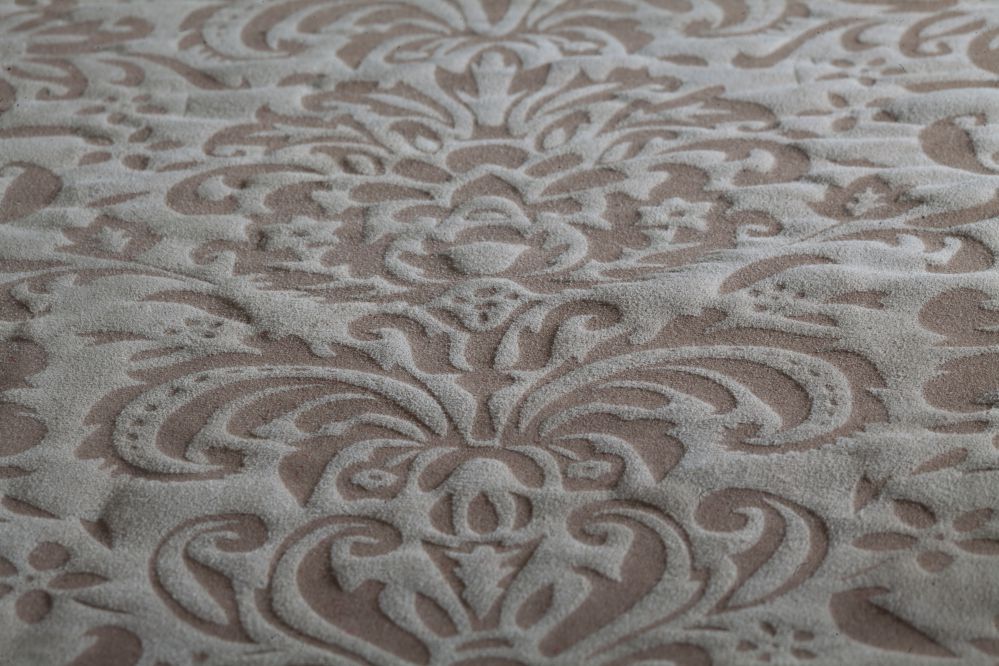
Laser engraving leather: an asset for the fashion and decorating industry
Laser engraving is one of the many applications of CO2 lasers. This process uses the energy delivered by the laser
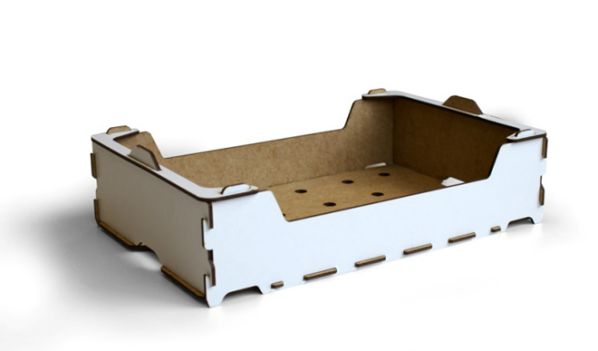
CO2 laser cutting of wood for the packaging industry
Laser cutting of wood-based products is one of the most important applications of CO2 lasers. Today, laser is a powerful,
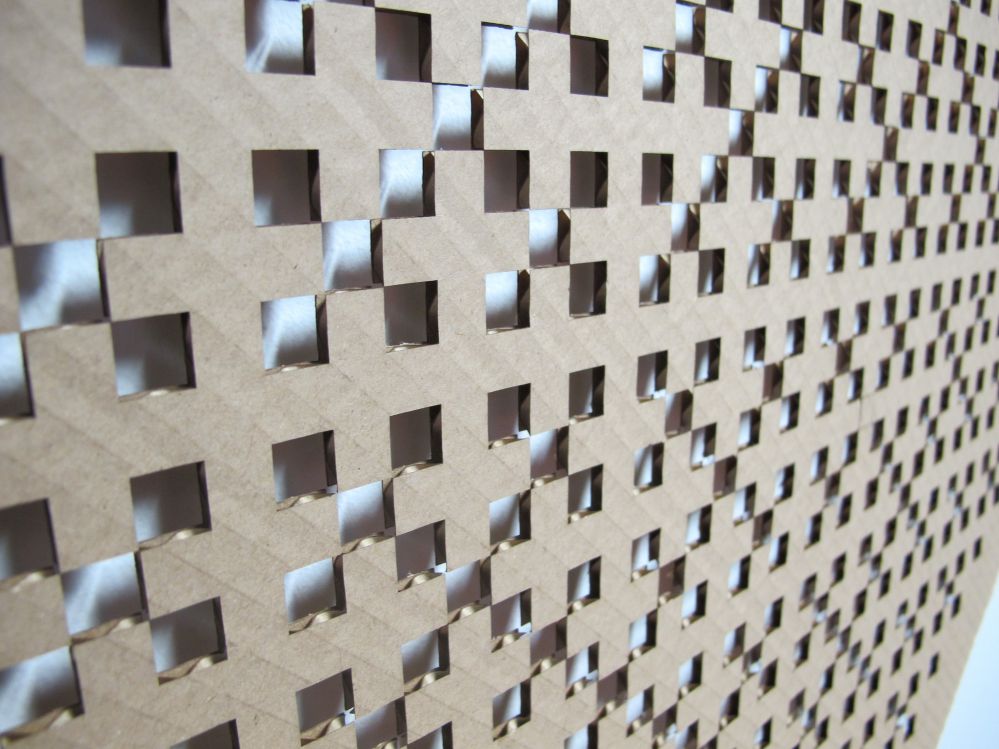
Laser cutting corrugated cardboard
Corrugated cardboard, also known as corrugated fiberbord or simply cardboard, is the most widely used packaging material. Its low production
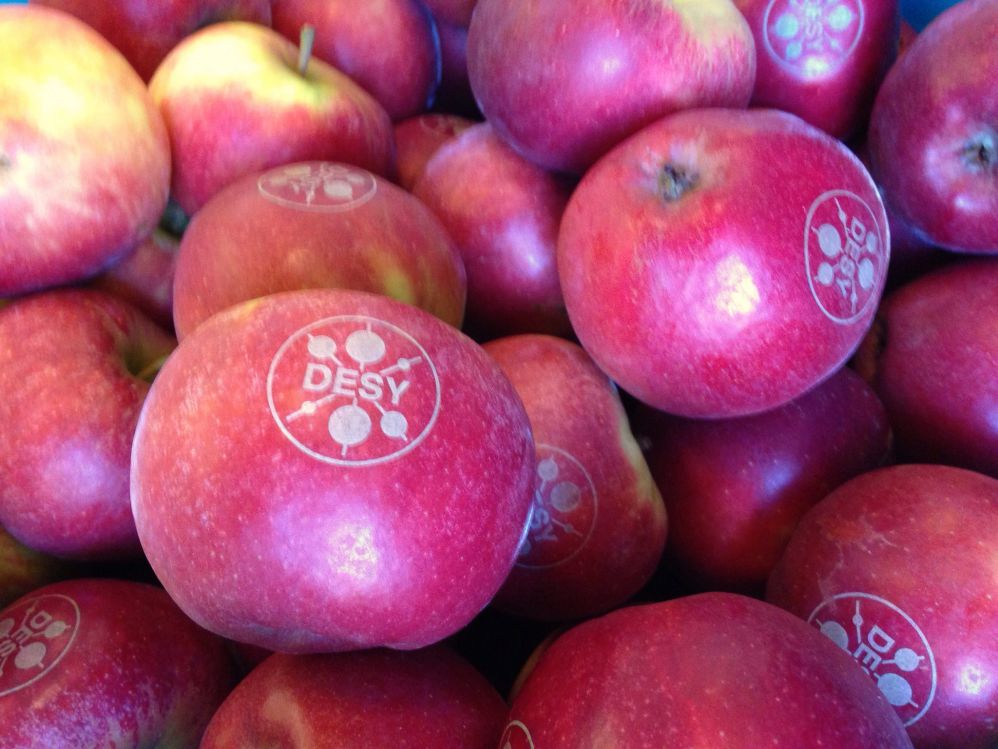
Laser labeling of food with laser marking
What if producers and distributors of fruit and vegetables stop using sticky labels? It’s not phantasy but reality: with laser
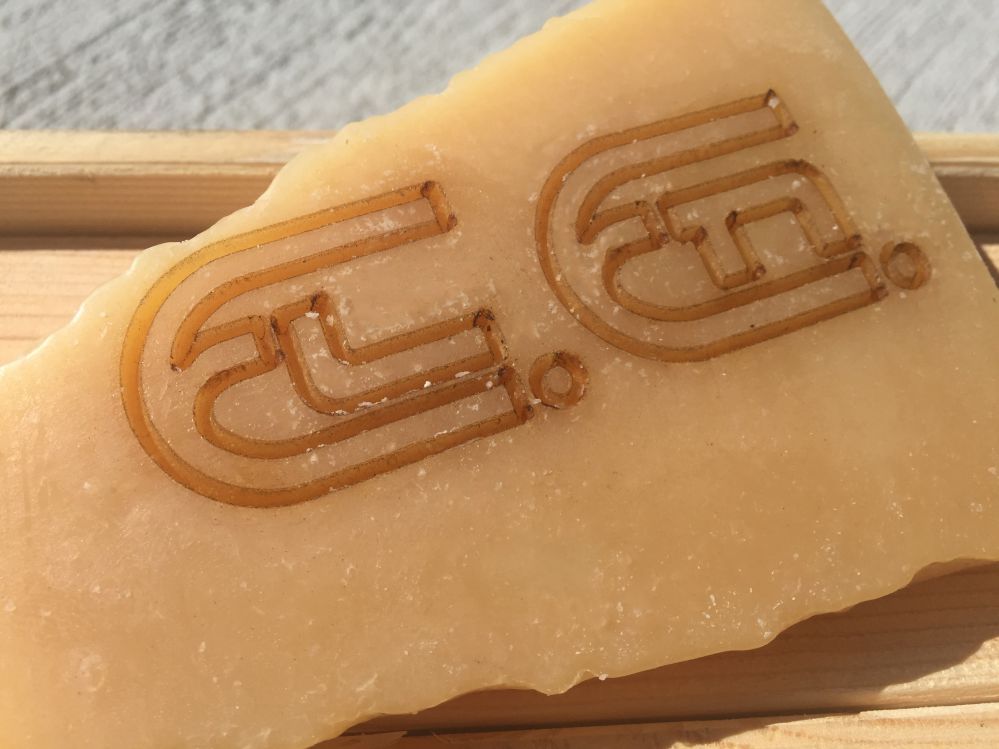
Laser Marking For Cheese and Ham
Laser labeling of food is a recent innovation that makes it possible to reduce production waste by replacing traditional food
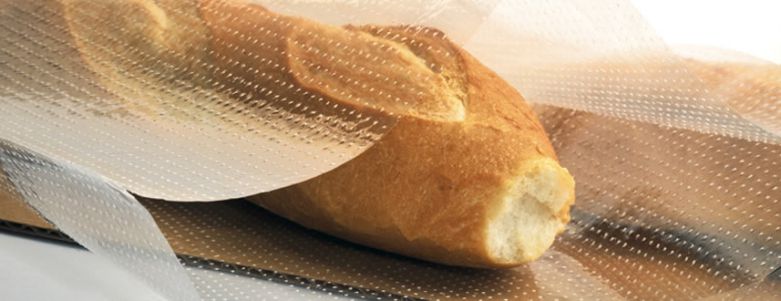
Laser micro-perforation of plastic bags for fresh products
One of the characteristics of CO2 lasers is that it allows you to carry out processes which were impossible to
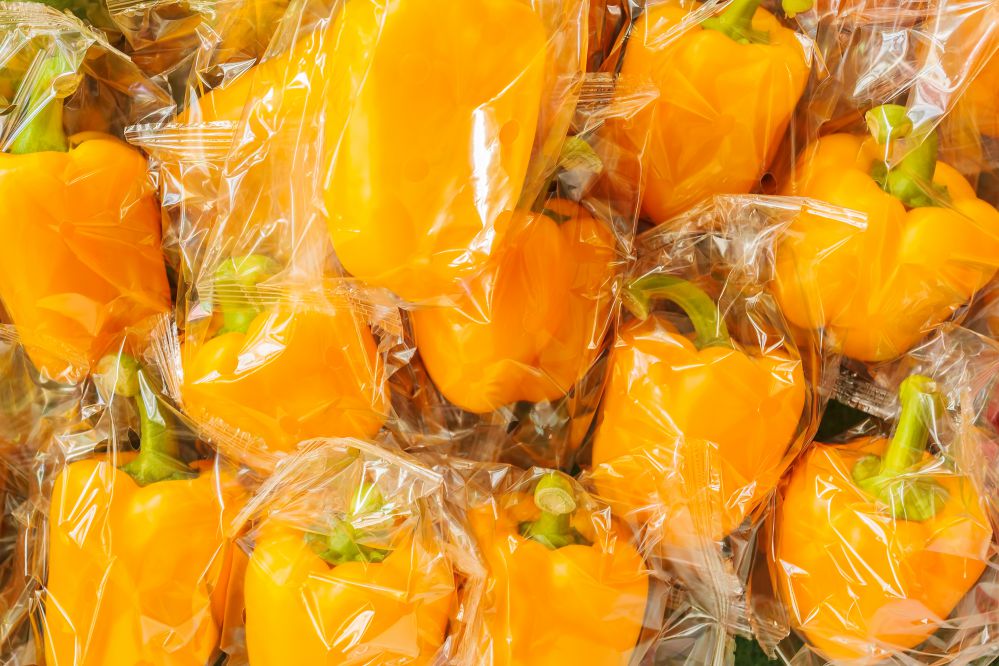
Laser digital converting for food packaging
The change in consumer behavior has augmented the demand for ready-to-use food. This, in turn, has resulted in the demand
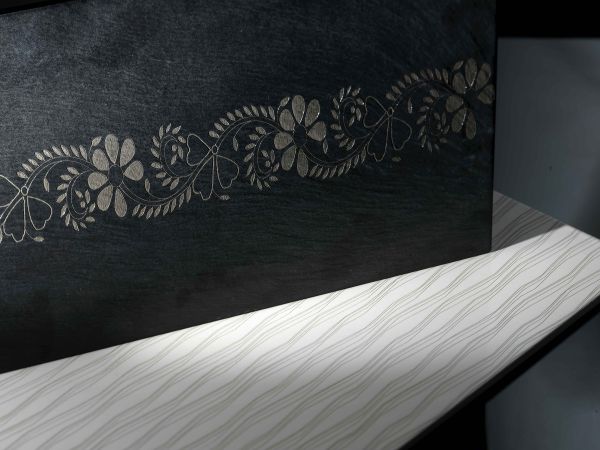
Laser engraving of ceramic tiles
The fashion, decoration, and design sectors are generally very competitive. They require a continuous stream of products and models to