Blade RF 333 G
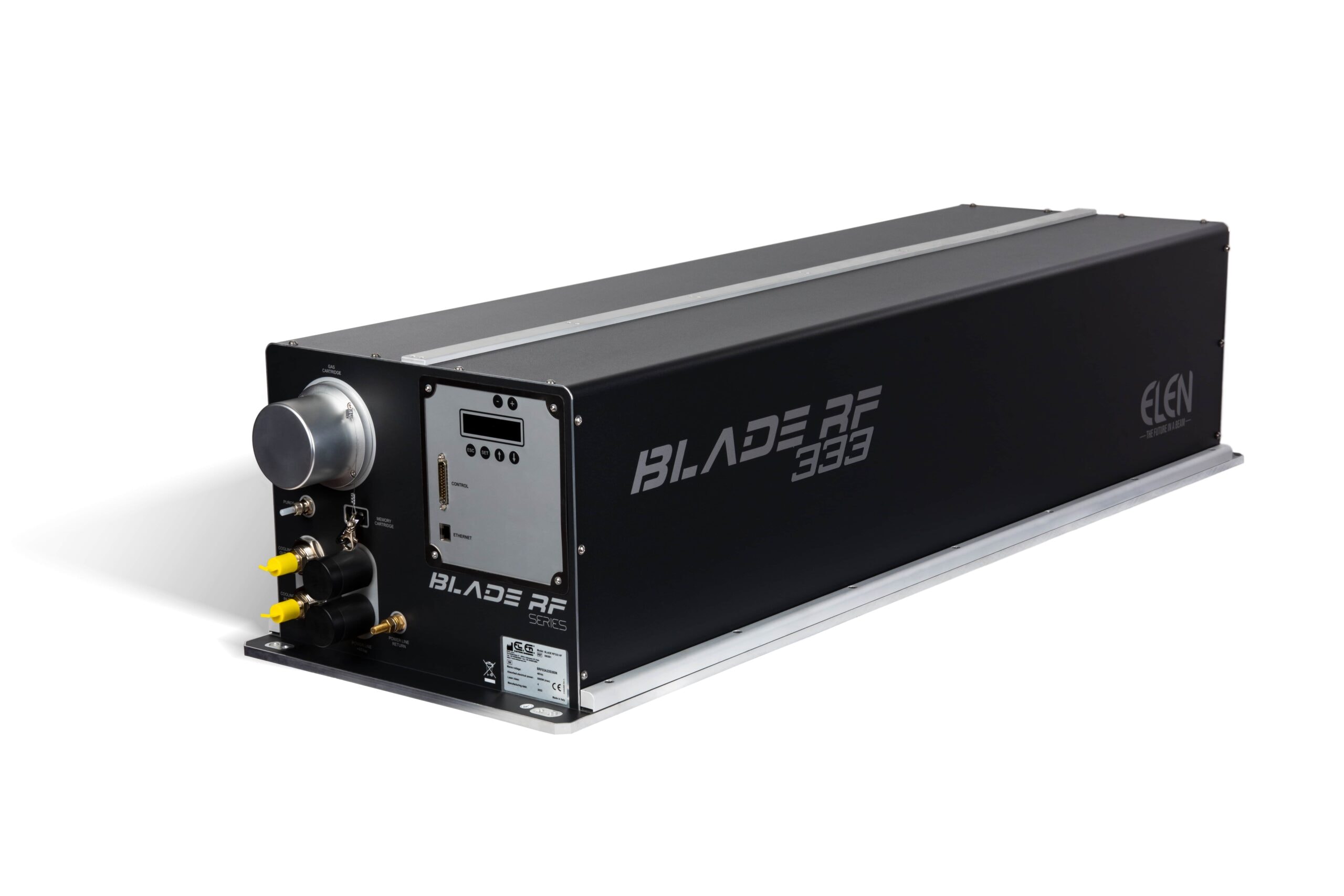
Rated power (W)
320 ÷ 350
Wavelength (μm)
9.3 ± 0.2
Stable and Reliable thanks to Self Refilling technology with wide range of wavelengths.
Stable and Reliable thanks to Self Refilling technology with wide range of wavelengths.
RF 333 Self-Refilling laser allows you to independently replace the gas cartridge and thus have stable laser parameters over time. The RF 333 G, with 9.3µm wavelength, is suitable for polymers ablation, such as hairpin cleaning on electric motor stators.
Materials
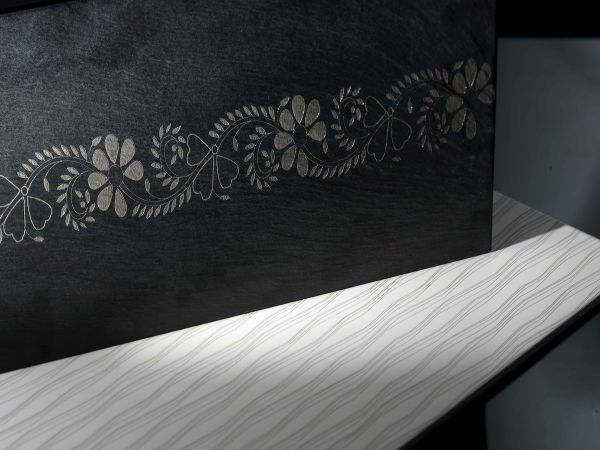
Ceramic & Alumina
Ceramic can be effectively cut and decorated with CO₂ laser sources. Owing to its high absorptivity of the 10.6 micrometers radiation, alumina (Al2O3) is the variety of ceramic that benefits the most from digital laser processing. Cutting of alumina is achieved by high-power laser pulses that vaporize the surface and produce perfect cuts. CO₂ laser can also be used for the decoration of tiles and other ceramic surfaces. With laser engraving, items are decorated with extreme precision, and according to the power of the CO₂ laser produced by El.En., contrasting and shading is achievable as well. These features make El.En.'s laser sources the perfect choice for applications such as cutting and decoration of ceramic and alumina.
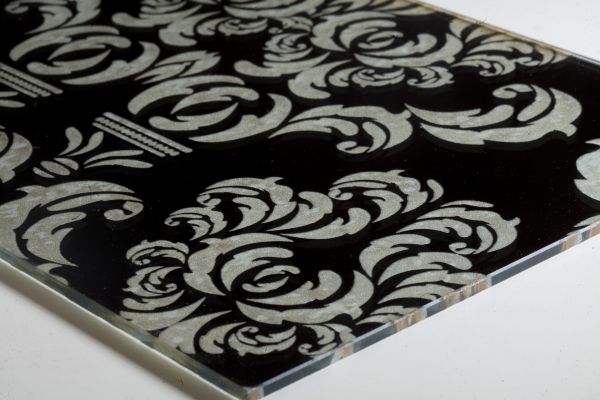
Glass & Quartz
When it comes to marking glass, nothing is better than CO₂ laser sources. Although it is transparent to visible light, glass absorbs the infrared light emitted by a CO₂ laser sources, resulting in a higher thermal efficiency and thus in cost reducing process. El.En.’s laser technology allows engravings in a simple, precise, and most of all lasting way, without changing the properties of glass. El.En. laser CO₂ laser sources and scanning heads are currently being used by many manufacturers in the fashion and machine tool industry. Learn about El.En.'s laser devices that will streamline your production processes.
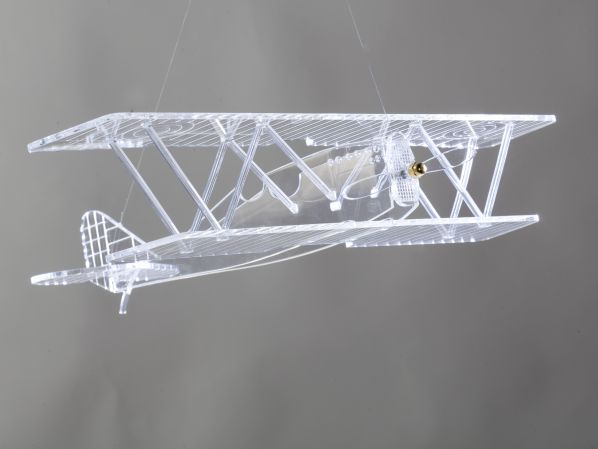
Plastic
Many types of plastic can be cut, drilled or marked by a CO₂ laser beam. Laser plastic processing gives you many advantages over traditional methods. When you're looking for precision in geometry and extreme operational flexibility, on close tolerances and on a micro-scale, any of the wavelengths emitted by a CO₂ laser beam can do the job. The final parts won't require refinement, avoiding any waste of base material and ensuring the highest level of accuracy. El.En.’s laser sources will process various types of Plexiglas: Clear, colored, textured, mirror-like or with silicate coating (methacrylate, PMMA). Acrylic fumes produced during the manufacturing will be sucked away and filtered during the process. El.En.'s CO₂ laser sources will enhance your productivity rate: Our ultimate goal is to make you produce faster and better.
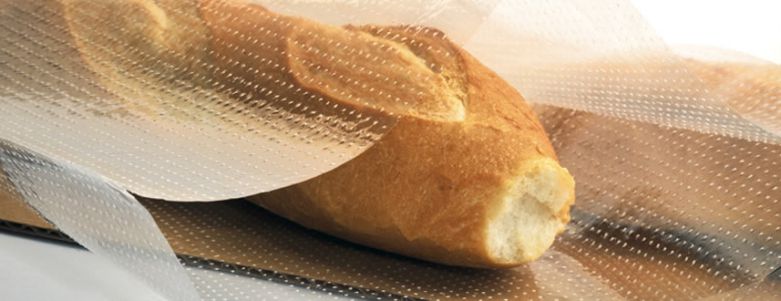
Plastic film
CO₂ laser is a groundbreaking tool for plastic film processing applications. Packaging, coating, digital converting markets will all benefit from a CO₂ laser solution. Being a non-contact process, laser is perfect when you have to deal with a base material as delicate as plastic film. It is a non-contact process: You won't waste or deform the plastic film and you will get the most accurate results achievable today in manufacturing this plastic material. El.En. laser scanning heads make this process possible: They will steer the laser beam emitted by the CO₂ laser source, focusing it precisely where it is needed. By doing so, you will achieve processing such as kiss cutting, micro perforation or welding in applications such as easy opening packaging, micro-perforated films for bread and vegetables.
Processing
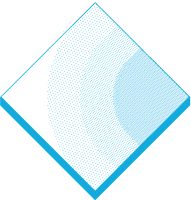
Laser Ablation
Laser ablation is indeed a versatile and precise technique for material removal from solid surfaces using laser energy. Laser ablation is highly precise, allowing for micron-level control over material removal. This precision is particularly advantageous in industries where selective material removal is crucial. The Minimal Heat Affected Zone (HAZ) is also a significat feature: laser ablation is a relatively low-heat process that minimizes the heat-affected zone, reducing the risk of thermal damage to the surrounding material. Materials like metals, polymers, ceramics, and composites can be laser ablated. This versatility makes it suitable for a broad spectrum of applications across different industries. In addition to material removal, laser ablation is widely used for surface cleaning. It can efficiently remove contaminants, oxides, or unwanted layers from surfaces, ensuring a clean substrate for subsequent processes.
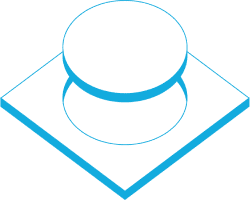
Laser Cutting
CO₂ lasers are tools that offer outstanding power and flexibility in laser material cutting applications. Laser cutting is a thermal process in which a laser, assisted by a gas, heats up the material, resulting in the alteration of its state. Laser material cutting advantages include great versatility regarding cutting speed, geometry, precision and accuracy of the cut. Plus, no further processing is required: The part you'll get will be perfectly finished. The typical 10.6 micrometers wavelength of CO₂ laser sources is readily absorbed by a wide range of materials. Metals, ceramic, wood, paper, glass, fabric, composites: a high-power CO₂ laser source will slice them like a knife. Owing to their beam quality and energetic efficiency, El.En's RF CO₂ laser sources are perfect for all those industries where achieving precision cutting is a strategic asset: Automotive, packaging, machine tool, lcd processing and others.
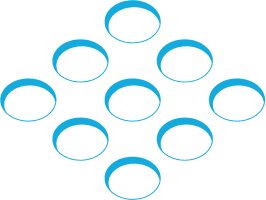
Laser Drilling
Imagine the possibility of making thousands of holes of any caliber in a short time. And without producing any chips and at exactly defined locations. That's exactly what a CO₂ laser source can do. Laser drilling is one of the most diffused laser applications, along with its sibling laser microperforation. Basically, the laser beam striking the surface of a plastic, metal or ceramic material, makes the base material evaporate. The holes resulting from this operation will have neat edges and won't need further processing operations. Furthermore, for drilling applications you can use the same laser sources you would use for cutting operations! El.En.'s laser sources have been engineered to work on metals, ceramic and plastic materials in machine tool, packaging, food, printing and decoration industries.
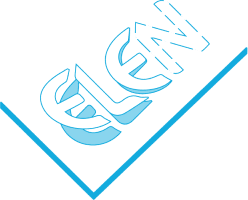
Laser Kiss-Cutting
Laser kiss cutting is a special cutting technique. It is very useful in the paper converting and label production industries: Laser kiss cutting aims at cutting only the top layer of a two-layered sheet instead of cutting through a sheet of paper, as in traditional laser cutting. The production of sticky labels is one of the main fields of application of this processing technique. The advantages of laser kiss cutting are remarkable: Since it is a non-contact process, there won't be any die or blade getting glued to the adhesive layer, avoiding the costs of tool cleaning. Futhermore, laser kiss cutting applications do not require special equipment: A single CO₂ laser source can achieve both laser kiss cut and laser cut through processing. Laser kiss cut is great to be employed in the paper and label industries, where it can be easily integrated into the printing process, but is also perfect for the coating and film industries.
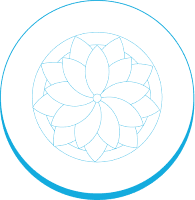
Laser Marking
High powered CO₂ lasers sources have become the standard tool for marking and engraving applications. Laser marking is a thermal process, which works through the ablation of a thin layer of the base material produced by a pulsed laser beam. All this results in a series of shallow pits on the surface that make the mark visible. When the marks made by laser are deeper we refer to laser engraving. Typically, lasers are used to mark bar codes, part codes and identification numbers, company logos and various graphics. Depending on the laser parameters, almost all types of materials can be successfully marked. Compared to traditional techniques laser marking offers high reliability, high speed, real time operability and low operating costs. El.En.'s sealed RF excited CO₂ laser sources have been engineered to achieve top grade results in marking applications: High laser beam quality, wide power ranges, high repetition rate and versatility. Hence, they are the perfect choice for applications in the packaging and electronic industries.
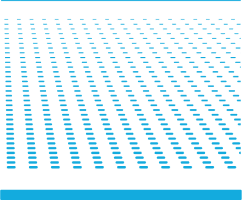
Laser Micro Perforation
Laser microperforation or laser microdrilling is the process of laser drilling micro holes on materials such as plastic films, paper and fabric. It is a subset of laser drilling processing techniques. Compared to mechanical micro perforation, laser offers speed, flexibility, resolution and accuracy. El.En.'s CO₂ laser sources operated in pulsed mode will pulse at a maximum frequency of 100 Khz to get perfectly round holes, with no debris or signs of recast. Owing to those characteristics, El.En.'s CO₂ laser sources are widely used in the food packaging industry, to create containers that will guarantee the quality of the food they store. Other applications are in the automotive industry to drill micro holes in tissues and in the fashion industry to make decorations based on micro-perforation.
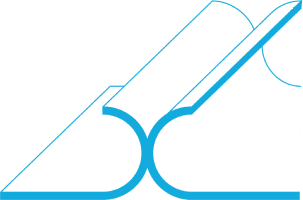
Laser Welding
Like traditional welding processes, laser welding aims to join two parts together. However, a CO₂ laser will do it better, faster and with greater accuracy. CO₂ lasers are succesfully used as a heat source for welding operations. The laser beam heats the edges of two parts to be processed: The heat melts the material, causing the two parts to fuse where they are contiguous. Its main field of applications is laser welding of plastic polymers. This processing technique can be used, for instance, to hermetically seal plastic bags, or to join together parts that are difficult to join with traditional welding tehcniques due to their layout. This makes laser welding excellent in all those applications where extreme precision is required even at micro-scales. But how is it performed? El.En.'s RF CO₂ laser sources coupled with an AZSCAN (for CO₂ laser) laser scan head, have all the key features to do the job. Beam quality and size, power range and components have been engineered to allow you to achieve great polymer welding results in the automotive, lcd and packaging industries.
Specifications
Rated power (W)
320 ÷ 350
Effective peak power (W)
750
Power stability (long term)
±5%
Wavelength (μm)
9.3 ± 0.2
Polarization
linear (parallel to base)
Beam diameter (1/e² at the exit)
7.0 ± 0.5
Beam divergence (1/e² full angle) (mrad)
2.0 ± 0.2
Maximum pulse frequency (kHz)
100
Pulse width range (μs)
2 ÷ 150
Maximum duty cycle
60%
Mode quality (M²)
< 1.1
Beam ellipticity
1.1 : 1
Optical pulse rise/fall time (μs)
< 50
Typical gas mix consumption (NL/year)
24 (2 cartridges per year)
Operating ambient temperature range (°C)
5 ÷ 35
Storage Temperature range (°C)
5 ÷ 50
Maximum humidity
Non condensing at inlet water temperature
Cooling
Heat load (W)
5000
Coolant temperature (°C)
23 ± 1
Water cooling input pressure (bar)
≤4
Water cooling flow rate (L/min)
12 ÷ 13
Dimension / Weight
Laser dimensions (LxWxH) (mm)
1327 x 420 x 309
RF power supply dimensions
integrated
Safety shutter
optional
Laser Weight (kg)
105
Electrical Power Requirements
Input voltage (Vᴰᶜ)
48 ± 1
Max current (A)
100
Peak Current (A)
120 for 3 ms max
Rated power (W)
320 ÷ 350
Effective peak power (W)
750
Power stability (long term)
±5%
Wavelength (μm)
9.3 ± 0.2
Polarization
linear (parallel to base)
Beam diameter (1/e² at the exit)
7.0 ± 0.5
Beam divergence (1/e² full angle) (mrad)
2.0 ± 0.2
Maximum pulse frequency (kHz)
100
Pulse width range (μs)
2 ÷ 150
Maximum duty cycle
60%
Mode quality (M²)
< 1.1
Beam ellipticity
1.1 : 1
Optical pulse rise/fall time (μs)
< 50
Typical gas mix consumption (NL/year)
24 (2 cartridges per year)
Operating ambient temperature range (°C)
5 ÷ 35
Storage Temperature range (°C)
5 ÷ 50
Maximum humidity
Non condensing at inlet water temperature
Laser dimensions (LxWxH) (mm)
1327 x 420 x 309
RF power supply dimensions
integrated
Safety shutter
optional
Laser Weight (kg)
105
Input voltage (Vᴰᶜ)
48 ± 1
Max current (A)
100
Peak Current (A)
120 for 3 ms max
Heat load (W)
5000
Coolant temperature (°C)
23 ± 1
Water cooling input pressure (bar)
≤4
Water cooling flow rate (L/min)
12 ÷ 13
Rated power (W)
850
Wavelength (μm)
10.6 ± 0.4
Peak Current (A)
260 for 3 ms max
Laser dimensions (LxWxH) (mm)
1327 x 420 x 309
Rated power (W)
850
Wavelength (μm)
10.6 ± 0.4
Peak Current (A)
260 for 3 ms max
Laser dimensions (LxWxH) (mm)
1327 x 420 x 309
Rated power (W)
320 ÷ 350
Wavelength (μm)
10.2 ± 0.2
Peak Current (A)
120 for 3 ms max
Laser dimensions (LxWxH) (mm)
1327 x 420 x 309
Rated power (W)
320 ÷ 350
Wavelength (μm)
10.2 ± 0.2
Peak Current (A)
120 for 3 ms max
Laser dimensions (LxWxH) (mm)
1327 x 420 x 309
Rated power (W)
1500
Wavelength (μm)
10.6 ± 0.4
Rated power (W)
1200
Wavelength (μm)
10.6 ± 0.4
High reliability and stability thanks to Self Refilling technology with optimal laser beam parameters
Rated power (W)
850
Wavelength (μm)
10.6 ± 0.4
High reliability and stability thanks to Self Refilling technology with optimal laser beam parameters
High reliability and stability thanks to Self Refilling technology with 850W average power
Rated power (W)
850
Wavelength (μm)
10.6 ± 0.4
High reliability and stability thanks to Self Refilling technology with 850W average power
High reliability and stability thanks to Self Refilling technology with 750W average power
Rated power (W)
750
Wavelength (μm)
10.6 ± 0.4
High reliability and stability thanks to Self Refilling technology with 750W average power
Stable and Robust thanks to Self Refillng technology, countless installations around the world prove its reliability
Rated power (W)
550
Wavelength (μm)
10.6 ± 0.4
Stable and Robust thanks to Self Refillng technology, countless installations around the world prove its reliability
High reliability and stability thanks to Self Refilling technology with wide range of wavelengths
Rated power (W)
320 ÷ 350
Wavelength (μm)
10.2 ± 0.2
High reliability and stability thanks to Self Refilling technology with wide range of wavelengths
High reliability and stability thanks to Self Refillng technology with wide range of wavelengths
Rated power (W)
320 ÷ 350
Wavelength (μm)
10.6 ± 0.4
High reliability and stability thanks to Self Refillng technology with wide range of wavelengths
Our Products are made with the utmost care. Nothing is left to chance: this is why we produce all the components of our devices in house.
Products
Three product series with high levels of customization to meet even the most demanding production requests.
Our Products are made with the utmost care. Nothing is left to chance: this is why we produce all the components of our devices in house.
Products
Three product series with high levels of customization to meet even the most demanding production requests.