GZ2520
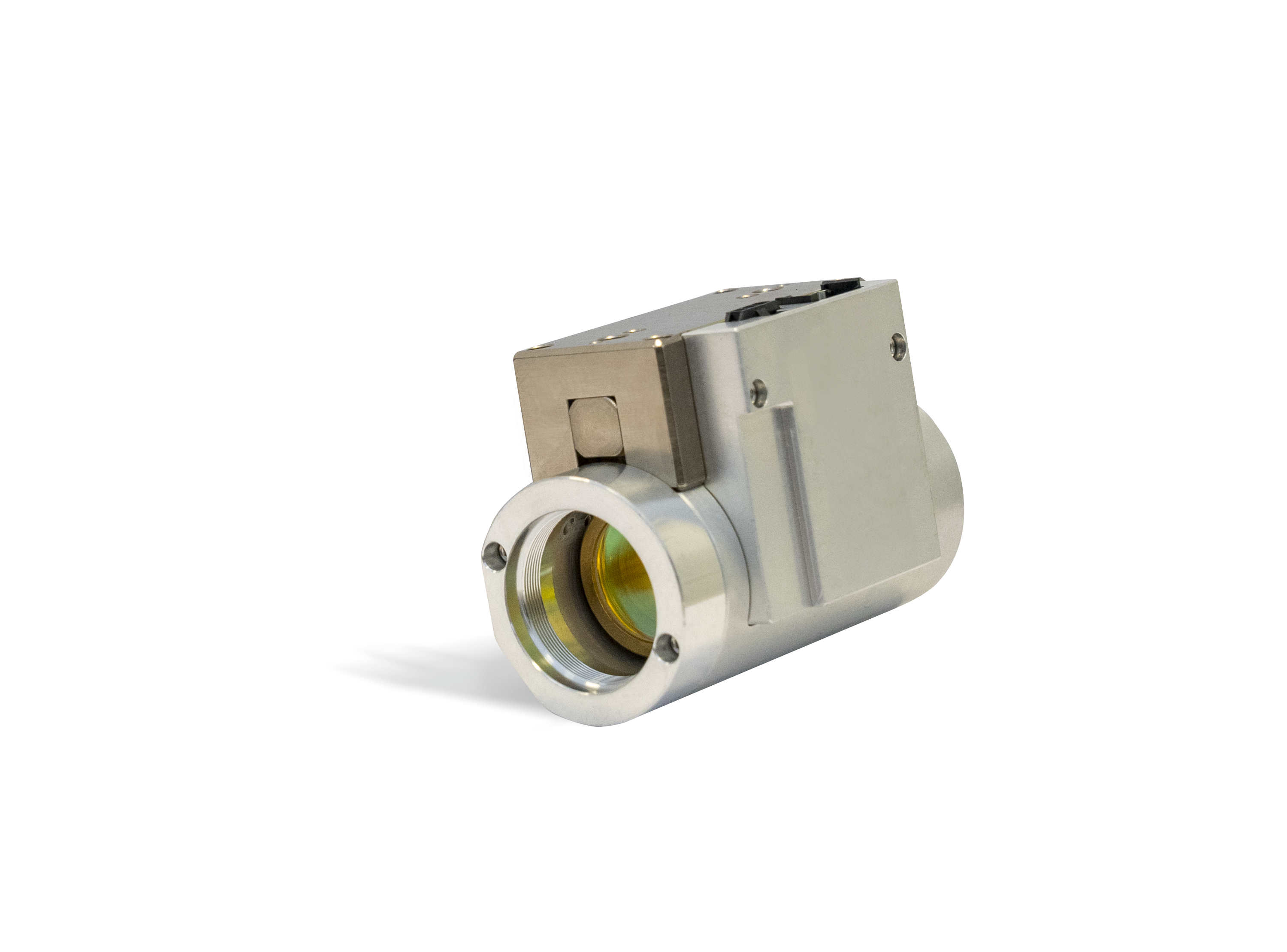
Optical aperture (mm)
24
Optimal Focusing for large laser beam
Optimal Focusing for large laser beam
Galvo Z Scan series, built by El.En in-house, is a versatile solution for laser processing applications, providing precise control over the laser focus in three dimensions and offering customization options to meet the specific needs of different applications. Dynamic and Precise Positioning to allow 3D Processing Capability and to replace expensive flat objectives with a wide range of product series offers a variety of sizes and optics designed to cater to different customer applications.
Materials
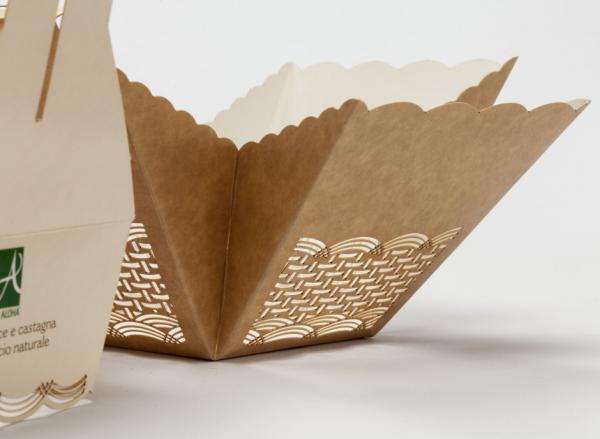
Cardboard & Corrugated
For some industries, the container is as important as the content. Cutting or marking cardboard sheets with CO₂ laser allows the creation of attractive packaging that can help better sell products. Whether your packaging is designed to showcase ripe blackberries or protect precious crystal glasses, El.En. laser sources will streamline your process. Laser cardboard processing gives you all the advantages of digital finishing: Cutting intricate designs with smooth edges and perfectly square joints, high-speed processing, accuracy and flexibility even on tight tolerances. No hard-tooling is required: Avoid the costs of designing tools, forget tool wear and periodic tooling substitution. Laser processing is no-contact and that's why it can be so fast and flexible and cost-effective.
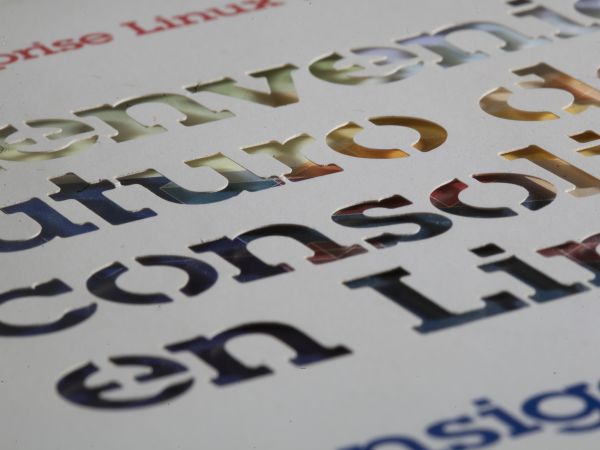
Paper / Label
Paper and cardboard respond very well to the wavelength emitted by CO₂ laser beams. That makes paper digital converting extremely efficient. Being a non-contact process, laser finishing avoids the risk of deformation or distortion of the base material, always ensuring clean cuts and square edges, even with the most intricate designs. For those reasons, cutting and marking are the obvious applications of laser paper processing. Owing to their accuracy, El.En.'s CO₂ laser sources are also used in applications such as laser kiss cutting and laser micro-perforation, especially in the packaging and decorating.
Processing
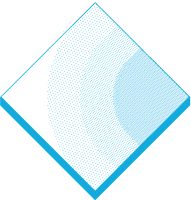
Laser Ablation
Laser ablation is indeed a versatile and precise technique for material removal from solid surfaces using laser energy. Laser ablation is highly precise, allowing for micron-level control over material removal. This precision is particularly advantageous in industries where selective material removal is crucial. The Minimal Heat Affected Zone (HAZ) is also a significat feature: laser ablation is a relatively low-heat process that minimizes the heat-affected zone, reducing the risk of thermal damage to the surrounding material. Materials like metals, polymers, ceramics, and composites can be laser ablated. This versatility makes it suitable for a broad spectrum of applications across different industries. In addition to material removal, laser ablation is widely used for surface cleaning. It can efficiently remove contaminants, oxides, or unwanted layers from surfaces, ensuring a clean substrate for subsequent processes.
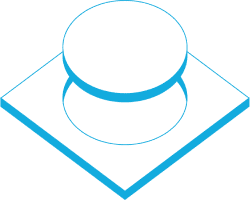
Laser Cutting
CO₂ lasers are tools that offer outstanding power and flexibility in laser material cutting applications. Laser cutting is a thermal process in which a laser, assisted by a gas, heats up the material, resulting in the alteration of its state. Laser material cutting advantages include great versatility regarding cutting speed, geometry, precision and accuracy of the cut. Plus, no further processing is required: The part you'll get will be perfectly finished. The typical 10.6 micrometers wavelength of CO₂ laser sources is readily absorbed by a wide range of materials. Metals, ceramic, wood, paper, glass, fabric, composites: a high-power CO₂ laser source will slice them like a knife. Owing to their beam quality and energetic efficiency, El.En's RF CO₂ laser sources are perfect for all those industries where achieving precision cutting is a strategic asset: Automotive, packaging, machine tool, lcd processing and others.
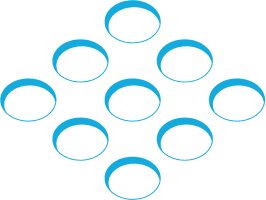
Laser Drilling
Imagine the possibility of making thousands of holes of any caliber in a short time. And without producing any chips and at exactly defined locations. That's exactly what a CO₂ laser source can do. Laser drilling is one of the most diffused laser applications, along with its sibling laser microperforation. Basically, the laser beam striking the surface of a plastic, metal or ceramic material, makes the base material evaporate. The holes resulting from this operation will have neat edges and won't need further processing operations. Furthermore, for drilling applications you can use the same laser sources you would use for cutting operations! El.En.'s laser sources have been engineered to work on metals, ceramic and plastic materials in machine tool, packaging, food, printing and decoration industries.
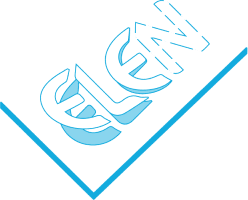
Laser Kiss-Cutting
Laser kiss cutting is a special cutting technique. It is very useful in the paper converting and label production industries: Laser kiss cutting aims at cutting only the top layer of a two-layered sheet instead of cutting through a sheet of paper, as in traditional laser cutting. The production of sticky labels is one of the main fields of application of this processing technique. The advantages of laser kiss cutting are remarkable: Since it is a non-contact process, there won't be any die or blade getting glued to the adhesive layer, avoiding the costs of tool cleaning. Futhermore, laser kiss cutting applications do not require special equipment: A single CO₂ laser source can achieve both laser kiss cut and laser cut through processing. Laser kiss cut is great to be employed in the paper and label industries, where it can be easily integrated into the printing process, but is also perfect for the coating and film industries.
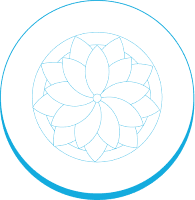
Laser Marking
High powered CO₂ lasers sources have become the standard tool for marking and engraving applications. Laser marking is a thermal process, which works through the ablation of a thin layer of the base material produced by a pulsed laser beam. All this results in a series of shallow pits on the surface that make the mark visible. When the marks made by laser are deeper we refer to laser engraving. Typically, lasers are used to mark bar codes, part codes and identification numbers, company logos and various graphics. Depending on the laser parameters, almost all types of materials can be successfully marked. Compared to traditional techniques laser marking offers high reliability, high speed, real time operability and low operating costs. El.En.'s sealed RF excited CO₂ laser sources have been engineered to achieve top grade results in marking applications: High laser beam quality, wide power ranges, high repetition rate and versatility. Hence, they are the perfect choice for applications in the packaging and electronic industries.
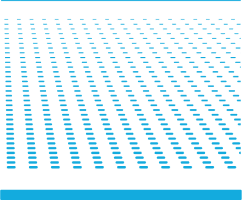
Laser Micro Perforation
Laser microperforation or laser microdrilling is the process of laser drilling micro holes on materials such as plastic films, paper and fabric. It is a subset of laser drilling processing techniques. Compared to mechanical micro perforation, laser offers speed, flexibility, resolution and accuracy. El.En.'s CO₂ laser sources operated in pulsed mode will pulse at a maximum frequency of 100 Khz to get perfectly round holes, with no debris or signs of recast. Owing to those characteristics, El.En.'s CO₂ laser sources are widely used in the food packaging industry, to create containers that will guarantee the quality of the food they store. Other applications are in the automotive industry to drill micro holes in tissues and in the fashion industry to make decorations based on micro-perforation.
Mechanical and Electrical specifications
Optical aperture (mm)
24
Linearity (%)
99.9% min
over 20mm
Scale drift (ppm/K)
100 max
Zero drift (μrad/°K)
10 max
Long term drift (% f.s./year)
200 max
Repeatibility (μrad)
5 max
Moving trolley excursion (mm)
20 Typical / 21 Max
Moving lens housing
Ø 1” * 4mm thickness Max
Moving trolley speed (mm/s)
1400 Max
Moving trolley acceleration (G)
25 Max
Setting time (ms)
3.6 @ Dx = 2mm Max
15 @ Dx = 20mm Max
Weight (g)
510 ± 10%
Optical aperture (mm)
24
Linearity (%)
99.9% min
over 20mm
Scale drift (ppm/K)
100 max
Zero drift (μrad/°K)
10 max
Long term drift (% f.s./year)
200 max
Repeatibility (μrad)
5 max
Moving trolley excursion (mm)
20 Typical / 21 Max
Moving lens housing
Ø 1” * 4mm thickness Max
Moving trolley speed (mm/s)
1400 Max
Moving trolley acceleration (G)
25 Max
Setting time (ms)
3.6 @ Dx = 2mm Max
15 @ Dx = 20mm Max
Weight (g)
510 ± 10%
Optical aperture (mm)
18
Our Products are made with the utmost care. Nothing is left to chance: this is why we produce all the components of our devices in house.
Products
Three product series with high levels of customization to meet even the most demanding production requests.
Our Products are made with the utmost care. Nothing is left to chance: this is why we produce all the components of our devices in house.
Products
Three product series with high levels of customization to meet even the most demanding production requests.